摘要:相对于轴流泵叶轮的不可切割性,在此我们赵忠介绍了用两种方法车削离心泵叶轮外径时,在改变泵性能上所产生的差别,通过分析解释了产生这种差别的原因,并提出了改进离心泵切削叶轮外径的方法。
一 前言
采用改变转速的方法可以得到不同工况时的水泵特性曲线。然而这种方法在实际应用中受到限制,因为大多数水泵是由交流三相异步电动机来驱动的。这种电动机的转速是不能随意改变的,若用变频调速则增加了设备费用。车削叶轮外径也能改变泵的特性,而且是一种简单易行的方法,这种方法只能用在需要减小水泵流量、扬程和功率的场合。切削叶轮外径的方法扩大了一台泵的使用范围,所以在单级离心泵上是普遍采用的方法。切割叶轮是依据泵理论中的相似准则,当用车削叶轮直径方法改变泵性能时,通常都是根据切割定律公式来计算的。试验表明如果按相似律计算的直径切割叶轮,往往都达不到期望的性能,叶轮切割得越多,实际性能与期望的性能之间的差距越大,以至于造成叶轮报废的损失。对新产品来说,往往要凭个人经验留有足够的余量,叶轮应分几次逐渐切割,每次切割后必须上试验台进行试验,这加大了试验的工作量,影响了试验工作效率的提高。
二、对叶轮的两种车削方法的试验
对一台50—32—315型单级单吸磁力泵进行了两种叶轮切割方法的性能试验,从中发现了值得思考的差别,现加以介绍。泵的叶轮在未切割时的直径D2=324mm,泵体隔舌处基圆直径D3=334mm,叶轮切割试验顺序如图1。 1) 图1a所示叶轮为原形尺寸,试验的性能工况点
图1叶轮外径切割图 (a)叶轮为原形尺寸(b)叶片外径车削到D2=324mm (c)叶片外径车D2=285mm (d)车削D 2=276mm (e)叶轮前后盖板直径从p2=305mn车削到 =276mm 1.叶片2.前盖板3.后盖板 为:Qa=6.8m3/h,Ha =152m,n=2950r/min,η=12%,因为用户要求在该流量下的扬程为H=135m,所以需对图1a所示叶轮外径进行车削以满足用户要求。
2) 图1b所示叶轮是按照Hb=135m要求,根据切割定律公式计算后,将叶轮外径遵照通常的做法,将叶轮的前后盖板和叶片的外径均车削到D2=305mm。其试验结果为:Qa =6.8m3/h,H=130m,n=2950r/min,显然实际扬程未能达到期望值。这是因为在切割叶轮时并不能单独地控制扬程。泵的实际工况点将从a点沿着切割抛物线ab自动地向下移动到 素(如图2)。此时扬程满足了要求而流量却小了,Qb < Qa为使流量达到要求,开大出口阀门调整流量到Qa,此时泵的工况点将沿着D2=305mm的Q-H曲线向右下方从b点移动到F,此时练的扬程肯定是小于b点的,Ht=130m< Hb=135m。这是因为离心泵的特性曲线是随着流量增加而扬程下降的固有特性所决定的。而离心泵的特性曲线下降形状又是与泵的比转数有的,离心泵的比转速范围相当宽广,所以按切割定律很难做出精确计算,必须在计算上留有足够的余量,余量的大小往往与个人的经验有关。
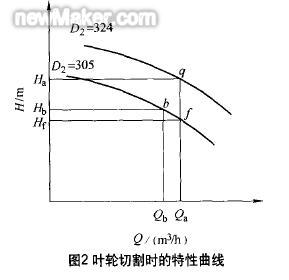
3) 图1c所示叶轮是将图1b所示叶轮的叶片外径车D2=285mm,而前后盖板外径不变。按切割定律公式Qc=QbDc/Db和Hc=Hb(Dc/Db)2来计算,可知图1c叶轮此时的工况点应当是Qc=6.35m3/h,Hc=113.5m。若使图1c所示的叶轮的流量调整到Qc=Qa=6.8m3/h时,则对应的扬程将应该是 Hc’< Hc=113.5m,理由正如图1b所示。但是,图1c所示叶轮的试验结果却是当Qc=6.8m3/h时对应的扬程Hc'=l19m>Hc=113.5m,这就是说不切削盖板的扬程要比切割定律计算值的扬程高出近5%。
4) 为了进一步证实这种效果,将图1cN示叶轮叶片外径再车削D2=276mm,而前后盖板外径保持不变,这就是图1dN示的叶轮。也用切割定律公式计算预测图ld所示的叶轮的工况点应当是Qd=6.15m3/h,Hd=106.5m。若使图1dN示的叶轮的流量也调节到Qd=Qa=6.8m3/h,则对应的扬程也将会是Hd’< Hd= 106.5m,理由同上。但是,图1d所示的叶轮的试验结果却是当Qd=6.8m3/h时对应的扬程Hd’=114.7m>Hd= 106.5m,也比切割定律的计算值要高出近8%。同时试验结果还表明图1b、图lc~图1d所示的三个叶轮在同一个流量点时泵的效率基本不变。
5) 图1eN示的叶轮是将叶轮前后盖板直径从D2=305mm车削到D2=276mm,这正像通常车削叶轮一样。此时图le所示叶轮的性能也以图1b所示叶轮对应的工况点来计算,预测其工况点将是Qe=6.15m3/h,He=106.5m。若使流量调节到Qe=Qa=6.8m3/h,试验结果表明此时He’=102.7m< He=106.5m。这种结果前面已分析过了,是情理之中的。值得注意的是图1d所示叶轮和图1e所示叶轮两者之间的差别仅仅在于前后盖板切与不切,可是两者在相同流量时,其扬程竞相差Hc'-He’=114.7-102.7=12m,其相对误差达10%,可见差别多么明显。
三 两种车削方法在性能上产生差别的原因
离心泵的研究对象是充满叶轮内两相邻叶片间的空间内液体质点的运动,液体微团是在一个受两个叶片及前后盖板所约束的流道内产生旋转运动的。切割定律是在认为叶轮在切割前后出口速度三角形的所有速度减小比例都与直径比D2'/D2 相同的假设条件下得出的。在离心泵中扬程是由叶片产生的,泵体的作用是叶片传递给液体的动能转换为压力能,它不产生扬程,它应该使进入泵体的液体水力损失最小。试验证明泵的水力损失主要发生在泵体内,所以泵的叶轮和泵体在设计计算时是相匹配的,决不是拿一个好的叶轮和随便找一个泵体只要能组装上就能得到一个性能优良得水泵。泵的叶轮直径D2 和泵体的基圆直径D3 之间也是根据最优转动间隙来确定的。理想的做法是叶轮的尺寸改变了,则泵体的尺寸也应该做相应的改变与之相匹配。例如图1中的基圆直径D3和蜗壳的断面面积大小都应当随着叶轮外径的减小而减小。但是这种要求在实际生产中是办不到的。
叶轮产生的扬程主要体现在叶轮出口处液体的绝对速度的圆周分量Vu2与叶轮出口处叶片的圆周速度u2的比值上。液体进入泵体后,设计优良的泵体将不破坏和改变这种比值。但是切削叶轮时同时切削前后盖板的做法使得泵体的基圆直径D3 和叶轮外径D2 之间的间隙加大,形成环形空间。环形空间的液体是从叶片上得到了能量的流出液体,这部分液体若不受外界力的干扰,它们将保持自己的速度矩,流进扩散锥管,将动能转换成压力能,此时泵体内的水力损失最小。但是叶轮前后盖板直径的切削,使得从叶片出口流出的液体受到泵腔内液体的混合和干扰。叶轮前后盖板与泵体内壁问构成了泵的前后泵腔,泵腔是因结构需要而形成的,它们不是泵内流动液体的通道。泵腔就好比是一个死水区,在叶轮盖板的作用下,泵腔内的液体质点在有限的空间内做既有圆周运动又有径向和轴向运动。泵腔中的液体的流态和叶片出口的液体流态完全不同,当盖板不切割时,可以认为盖板将泵腔内的液体与叶片出口的液体隔离开来免受干扰。当盖板在叶轮切割时,切割量越大,则泵腔内液体对叶片出口液体的流动干扰就越大,结果就是水力损失越大,扬程降低得越多,本试验的结果证实了这一判断。
四、结论
1)试验是在一台低比转数离心泵上进行的,试验结果表明两种切削方法,在相同流量点,扬程可相差5%-10%。因为离心泵的比转数范围很广,所以这个扬程相差百分比并不具有广泛的代表性。而真正有意义的是不车削盖板的方法,满足和提高了切割定律的使用条件和精度。
2)只切叶片不切盖板的切割方法是一种有益而无害的方法,因为这种方法使泵腔内的液体对叶轮出口液流的影响降低到最小。试验表明,盖板直径不减小并不会造成泵的圆盘摩擦损失增加。因为圆盘摩擦损失不仅仅表现在叶轮盖板的直径上,它还与泵腔内液体所耗能量有关,后者才是损失的主要部分。
济南泰达泵业专业生产各型立式化工轴流泵,卧式轴流泵,高温熔盐泵、高温液下泵、熔盐液下泵、高温轴流泵、熔盐轴流泵,具有运行稳定可靠、噪音低、节能、寿命长等优点。
网址:www.jnzxby.com E_mail:jnzxpump@163.com
联系电话:0531-87970633 Fax:0531-87970632 |